Industrial Visit - Mechanical Engineering
Date of the Event | Mar 19, 2025 Group I - 10.15 AM & II - 02.15 PM |
Resource Person | Mr. Dipak Nikam |
Designation | Production Process In charge at Oetiker Group India |
Organization | Oetiker India Private Limited, Patalganga MIDC, Raigad |
Targeted Beneficiaries | Second Year Diploma in Mechanical Engineering students |
Targeted Course | Production Processes and Metrology & Measurement |
Number of Beneficiaries | 48 students |
Faculty In-charge | Prof. Arjun Deshmukh, PHCET - Diploma |
Report Overview
The industrial visit hosted by Mr. Dipak Nikam, Production Process In charge at Oetiker India, offered valuable insights into the company’s advanced manufacturing processes and data collection methods. Mr. Nikam demonstrated how Oetiker uses automation machine systems like Slitter, Oscillator, Ingyu, Finzer, and BMS for real-time data collection, enhancing efficiency. He also highlighted the role of IoT, AI, and Lean manufacturing tools like MOST Study and Kaizen in streamlining operations and improving product quality. Additionally, FMEA, VSM, and real-time quality control systems were discussed as key components in optimizing processes.The visit was led by Prof. Arjun Deshmukh, Faculty In-charge from PHCET – Diploma, guided the students for these Industrial Visit.
Profile of the Source Person
Mr. Dipak Nikam, a Mechanical Engineering graduate, brings over 6 years of experience in the manufacturing industry. As the Production Process In charge at Oetiker India Private Limited in Patalganga MIDC, he specializes in both heavy and light press shops (Mechanical + Hydraulic) and has expertise in systems like Slitter, Oscillator, Ingyu, Finzer, and BMS. His background includes operations, production, and tool maintenance with Progressive & Compound Tools, and he excels in resolving quality, process, and technical issues.
Well-versed in Lean manufacturing, IATF, ISO, MSES, and MSIL audits, Mr. Nikam is currently pursuing Lean Six Sigma Green Belt certification. He has earned recognition, including the CII National First Prize for the SMED Project and Best Kaizen, and is skilled in using FMEA and VSM with the DMAIC methodology. He also holds ISO certification in the SAP MM module.
Key Points of the Expert Talk
The industrial visit began with an introduction to Oetiker India, covering the company’s role in producing high-quality clamps and rings for various industries. Visitors learned about the Patalganga MIDC facility and its significance in the global supply chain of precision clamps. Next, Mr. Nikam showcased Oetiker’s diverse product range, including Ear Clamps, Low Profile Clamps, Multi Crimp Rings, Worm Drive Clamps, Strap Clamps, V Clamps, and Colour Coded ID Clamps. He focused on key products such as DualHook Adjustable Ear Clamps, ToothLock Ear Clamps, and various StepLess Ear Clamps, including next-generation and light-fit models, along with 1-Ear Clamps with Mechanical Interlock, WingGuard Strap Clamps, and unique solutions like 1-Ear Clamps with Stud.
The visit provided insight into Oetiker’s manufacturing process, featuring advanced systems like Slitter, Oscillator, Ingyu, Finzer, and BMS. Visitors explored both mechanical and hydraulic press shops and learned about the company’s high standards for quality control and product testing, ensuring compliance with IATF, ISO, MSES, and MSIL standards.
Mr. Nikam also discussed Lean manufacturing practices, including MOST Study and Kaizen techniques that optimize processes. He highlighted successful projects, such as winning the CII National First Prize for SMED and Best Kaizen, demonstrating Oetiker’s commitment to innovation.
The visit covered Mr. Nikam’s expertise in problem-solving using FMEA, VSM, and the DMAIC methodology to address process and quality issues. He also shared Oetiker’s on-going focus on Lean Six Sigma and automation as part of its commitment to continuous improvement.
Innovative Ideas, Strategies, or Technologies Mentioned
Mr. Nikam discussed how Oetiker uses automation machine systems like Slitter, Oscillator, Ingyu, Finzer, and BMS to collect real-time data, enhancing production efficiency. He explained the role of IoT and smart manufacturing technologies in tracking machine performance and enabling predictive maintenance. Mr. Nikam also highlighted how data analytics and AI detect inefficiencies and predict failures, improving operational efficiency.
He showcased Lean manufacturing tools like MOST Study and Kaizen for streamlining workflows and reducing waste. He further described how FMEA and VSM tools help identify and resolve process issues, while real-time quality control systems ensure product consistency. Additionally, Mr. Nikam shared how digital dashboards provide real-time production metrics and cloud-based data systems enable collaboration across departments. Finally, he discussed how Lean Six Sigma initiatives use data to drive continuous improvement and reduce process variability, ensuring high-quality standards at Oetiker.
Conclusion
The industrial visit to Oetiker India provided an insightful look into how modern technologies and data-driven strategies are transforming manufacturing processes. Through the implementation of automation systems, IoT, AI, Lean tools, and real-time monitoring, Oetiker ensures operational efficiency, product quality, and continuous improvement.
The session effectively demonstrated how data collection and analysis play a crucial role in optimizing processes and driving innovation in the manufacturing sector. The visit highlighted Oetiker’s commitment to staying at the forefront of industry advancements, making it an excellent example of modern manufacturing practices that prioritize quality, efficiency, and sustainability.
Date of the Event | March 13, 2025, 01:00 PM |
Resource Person | Mr. Uday Gothivarekar |
Designation | Plant Head |
Organization | Antony Garages Private Limited, Patalganga MIDC, Raigad |
Targeted Beneficiaries | Second Year Diploma in Mechanical Engineering students |
Targeted Course | Production Processes and Manufacturing Technology |
Number of Beneficiaries | 58 students |
Faculty In-charge | Prof. Arjun Deshmukh, PHCET - Diploma |
Report Overview
The Industrial Visit to Antony Garage Private Limited, located in Patalganga MIDC, Raigad, Maharashtra, was organized for the second-year Diploma in Mechanical Engineering students under the supervision of Prof. Arjun Deshmukh. The visit was scheduled on March 13, 2025, at 01:00 PM, with the aim of offering students’ practical exposure to advanced manufacturing techniques, production processes, and automotive technologies.
The source person for the visit was Mr. Uday Gothivarekar, the Plant Head at Antony Garages Private Limited, who led the session and provided valuable insights into the operations of the company.
Profile of the Source Person
Mr. Uday Gothivarekar, the Plant Head at Antony Garages Private Limited, has over 30 years of experience in automotive production management. His career has seen him hold various key positions, such as Production Manager at Von Automobile Nig. Ltd in Lagos, Nigeria, and Bharat Coach Builders Pvt. Ltd in Panvel, Maharashtra. Mr. Gothivarekar’s wealth of experience, particularly in automotive manufacturing and production management, made him an invaluable source of knowledge for the students during their visit. His leadership in the automotive industry and expertise in manufacturing practices contributed significantly to the educational value of the visit.
Key Points of the Expert Talk
During the industrial visit, Mr. Uday Gothivarekar provided an in-depth overview of the manufacturing processes employed at Antony Garages. He explained the various stages of production, from assembly line operations such as welding, body construction, and painting, to sub-assembly processes involving the chassis, body, engine, and transmission.
The students gained a deeper understanding of how complex automotive production can be and how each stage contributes to the final product. One of the significant aspects discussed was theextensive testing and quality control procedures employed by the company. Mr. Gothivarekar emphasized the importance of crash testing, road testing, structural testing, and vibration and durability testing, which ensure that the final product meets the required safety and performance standards. The visit also highlighted Antony Garages’ commitment to sustainability. Mr. Gothivarekar shared insights into the company’s use of electric bus technology, energy-efficient manufacturing processes, and the adoption of recycled materials in production. These efforts align with the global trend of reducing the environmental footprint of industrial manufacturing. Another key discussion was on the materials used in the manufacturing process. Mr. Gothivarekar explained the significance of using high-strength steel, aluminum alloys, composite materials for weight reduction, and eco-friendly interior materials to meet both performance and sustainability standards.
Finally, the expert talk covered the importance of supply chain management. Antony Garages works closely with various suppliers to ensure the timely delivery of high-quality components like engines, axles, and electronics. Mr. Gothivarekar emphasized how integrating suppliers effectively is crucial to maintaining production schedules and ensuring product quality.
Innovative Ideas, Strategies, or Technologies Mentioned:
During the visit, the students were introduced to several innovative ideas and strategies used in modern automotive manufacturing. Mr. Gothivarekar discussed how Antony Garages has embraced advanced practices in manufacturing process innovations, ensuring that their production lines remain efficient and capable of meeting high-demand specifications.
The company’s approach to testing and quality control also incorporated new technologies and techniques, ensuring their vehicles meet rigorous standards for safety and durability. In terms of sustainability, Antony Garages is leading the way in integrating electric vehicle technology into their product lineup and incorporating energy-efficient manufacturing processes, which reduce waste and improve overall efficiency. The materials used in the manufacturing process were also at the forefront of the discussion, with Mr. Gothivarekar highlighting the shift toward lighter, more durable materials such as aluminum alloys and composites. This not only improves the performance of the vehicles but also reduces their environmental impact. Supply chain management strategies were discussed in detail, emphasizing the need for strong relationships with key suppliers to ensure the seamless integration of components like engines, axles, and electronics. These strategies are crucial to achieving both efficiency and quality in production.
Conclusion
The industrial visit to Antony Garages Private Limited was an eye-opening experience for the students, offering a unique opportunity to see the application of theoretical concepts in the real world. From advanced manufacturing processes to cutting-edge technologies in sustainability, the visit provided a comprehensive overview of modern automotive production.
Mr. Uday Gothivarekar’s expert insights helped students understand the complexities of automotive manufacturing, supply chain management, and quality control. Overall, the visit was a valuable educational experience that bridged the gap between classroom learning and industry practices.
Date of the Event | February 25, 2025, 10:15 AM |
Resource Person | Mr. Ajit Parab |
Designation | Head Research and Development |
Organization | Swegon Bluebox India Private Limited, Taloja MIDC |
Targeted Beneficiaries | Third Year Diploma in Mechanical Engineering students |
Targeted Course | Capstone Project Execution |
Number of Beneficiaries | 10 students |
Faculty In-charge | Prof. Arjun Deshmukh, PHCET - Diploma |
Report Overview
On February 25, 2025, the Department of Mechanical Engineering at PHCET organized an industrial visit for third-year Diploma students to Swegon Bluebox India Pvt. Ltd., located in Taloja MIDC. The visit aimed to provide students with practical insights into HVAC system design, optimization, and energy-efficient technologies in the real-world setting of a leading industrial company.
Prof. Arjun Deshmukh, the faculty in charge of the Diploma program, oversaw the event, ensuring that students received a valuable learning experience. The industrial visit, which involved ten students, offered an opportunity to witness firsthand the complexities of HVAC systems and their components, while also bridging the gap between academic knowledge and industrial application.
Profile of the Source Person
The visit was addressed by Mr. Ajit Parab, the Head of Research and Development at Swegon Bluebox India Pvt. Ltd. With a wealth of experience in the HVAC industry, Mr. Parab is highly specialized in HVAC system design, optimization, and energy-efficient technologies. His expertise spans areas such as heat pumps, HVAC control systems (including DDC and BAS), Variable Refrigerant Flow (VRF) systems, and advanced refrigeration cycles.
Mr. Parab is also proficient in performance testing and simulation techniques, including Computational Fluid Dynamics (CFD) and lab testing. In addition to his technical skills, he is well- versed in HVAC regulatory standards like ASHRAE and ISO. His work in smart HVAC integration and IoT has significantly contributed to the development of innovative and energy-efficient solutions in the industry, making him an ideal resource for guiding students interested in the future of HVAC technologies.
Key Points of the Expert Talk
During the industrial visit, Mr. Ajit Parab shared his deep knowledge of HVAC systems, focusing on the importance of monitoring and analyzing key parameters in both air-cooled and water-cooled systems. He discussed various data points essential for optimizing the performance and efficiency of HVAC systems, such as chamber ambient temperature, evaporator water inlet and outlet temperatures, suction pressure, and compressor performance. These parameters are critical for maintaining the system’s overall efficiency, and Mr. Parab emphasized how understanding these variables can help in improving energy consumption and system longevity. He also provided insights into the significance of suction line temperature, discharge pressure, and compressor power consumption, explaining how these factors contribute to the proper functioning of the system. Students were shown practical examples of how real-time data collection from these variables could be used to assess and fine-tune HVAC systems, demonstrating the relevance of such practices in their future careers.
Innovative Ideas, Strategies, or Technologies Mentioned
Mr. Ajit Parab highlighted several innovative ideas and technologies used at Swegon Bluebox India Pvt. Ltd., focusing on advanced methods for collecting and analyzing data in HVAC systems. One notable innovation discussed was the use of IoT-based systems for smart HVAC integration, which allows for real-time monitoring of critical parameters.
By using advanced sensors and automation, the company can collect detailed data on factors like evaporator water flow, suction superheat, and compressor efficiency. These technologies enable continuous system optimization, predictive maintenance, and energy efficiency improvements.
Mr. Parab also explained how the integration of Variable Refrigerant Flow (VRF) systems contributes to better energy management and more adaptable climate control solutions in industrial environments. He further emphasized the importance of maintaining HVAC systems in line with regulatory standards such as ASHRAE and ISO, ensuring that performance and efficiency remain at the highest levels. Through these discussions, students were exposed to the practical application of modern HVAC technologies and how they can be leveraged to achieve sustainability and energy efficiency in the industry.
Conclusion
The industrial visit to Swegon Bluebox India Pvt. Ltd. proved to be an invaluable learning experience for the third-year Diploma in Mechanical Engineering students. Under the guidance of Mr. Ajit Parab, the students were able to witness firsthand the practical applications of HVAC system design, optimization, and the implementation of energy-efficient technologies in a real-world industrial setting. The insights shared by Mr. Parab, particularly in terms of data collection, system optimization, and smart HVAC integration, enhanced the students’ understanding of the complexity and significance of these technologies in modern-day engineering.
By exploring advanced systems such as VRF, heat pumps, and IoT integration, students gained a deeper appreciation for the innovations shaping the HVAC industry. This visit not only bridged the gap between theoretical knowledge and practical application but also inspired students to think critically about the role of technology in shaping sustainable and energy-efficient solutions in the field of mechanical engineering.
Date: 27th September, 2024
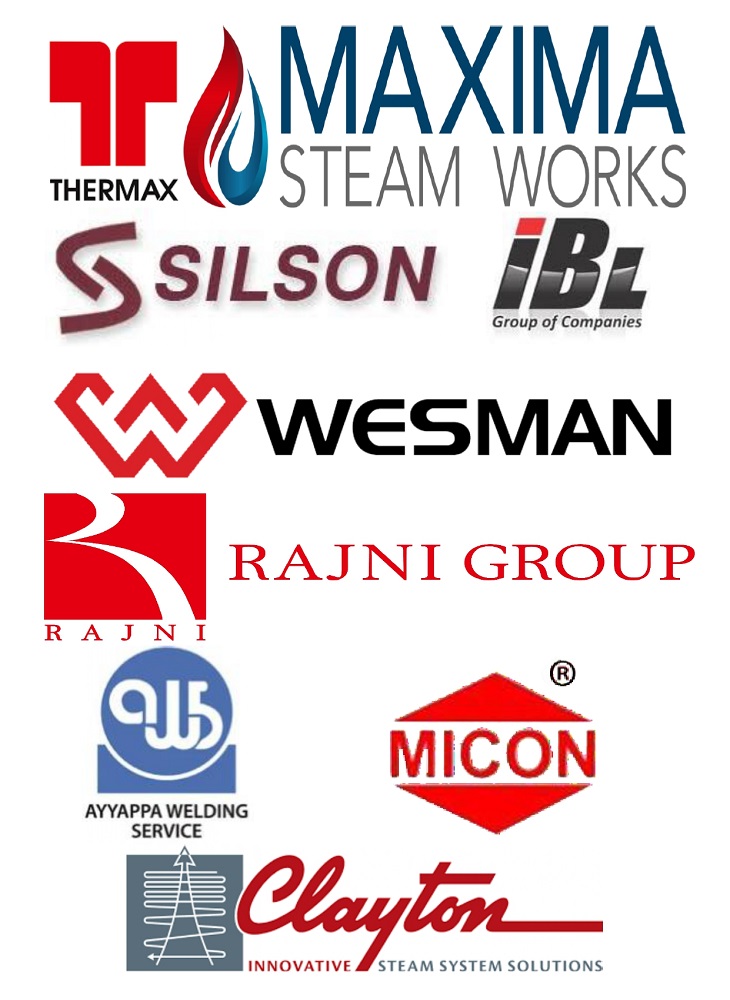
Date: 23th March, 2024
Date: 23th March, 2024
Date: 13th April, 2023
Date: 24th February, 2023
Date: 8th April, 2022
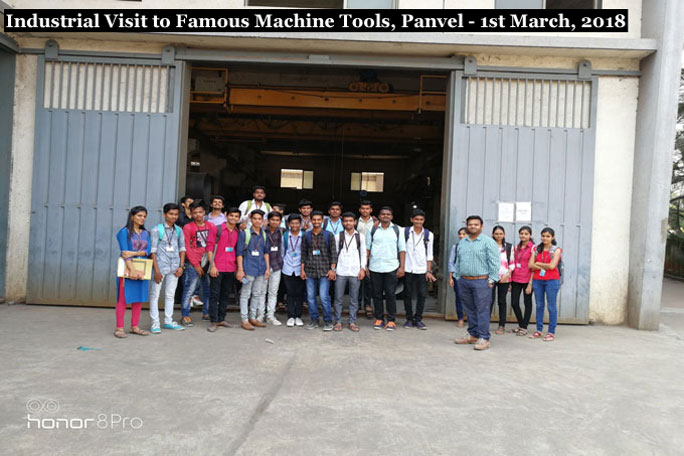
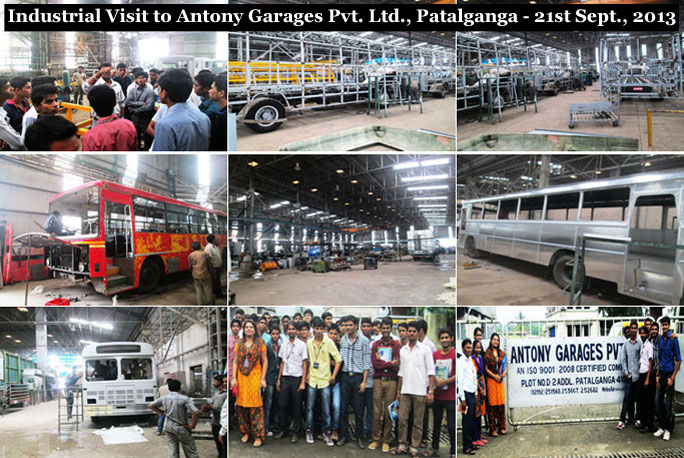